Hybrid Battery Reconditioning
HBR - Hybrid Battery Reconditioning
At HBR, we offer High-Quality, Low-Cost Hybrid Vehicle Battery Packs. At HBR, we use High-Tech and Sophisticated Equipment to Test, Analyze, and for hybrid battery reconditioning. We carefully assemble every Battery Pack in-house and subject them to stringent testing. We remanufacture and balance reconditioned modules into Hybrid Battery Packs.
Our latest process for reconditioning hybrid batteries brings old batteries back to life! We use original manufacturer (OEM) modules and provide a Standard 12-Month Warranty with optional extensions on All Our Hybrid Reconditioned Packs. If you are an auto shop or parts dealer looking for hybrid battery solutions, please call HBR. We recondition battery modules using the latest Technology and Equipment for Hybrid Batteries.
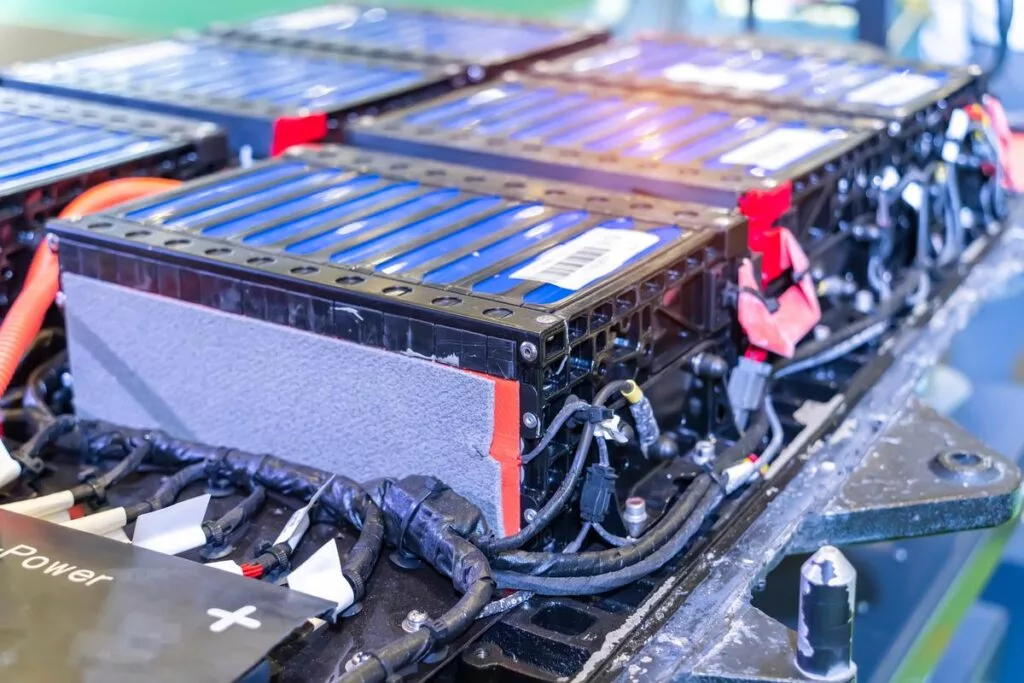
Why hyprid battery Reconditioning ?
01
Assessment and Diagnosis
Assess battery health through diagnostics to ascertain the feasibility of reconditioning.
02-
Reconditioning Process
Improve battery performance by balancing cells, cycling, and, if necessary, replacing individual cells.
03-
Testing and Verification
Conduct a comprehensive test on the reconditioned battery to verify enhanced capacity and reliability.
How Hybrid Battery Reconditioning Work ?
The process of hybrid battery reconditioning is aimed at restoring the performance and capacity of a hybrid vehicle’s battery pack. This approach serves as an alternative to outright replacement, and is geared towards prolonging the battery’s life and improving its efficiency.
To achieve this, reconditioning is typically performed on hybrid battery packs that have experienced reduced capacity, performance, or other issues due to cell degradation or imbalances. Here’s how reconditioning generally works:
Diagnosis:
The initial step is to first diagnose the battery pack’s condition. This process involves using specialized diagnostic tools and software to assess the state of each individual battery cell within the pack. The primary objective is to identify weak or degraded cells that are adversely affecting the overall performance of the battery.
Balancing:
A critical step in reconditioning involves balancing the battery pack. This process entails ensuring that all cells have a similar state of charge and capacity. Cells that are significantly weaker than others can lead to reduced performance and can accelerate the degradation of the entire pack. Additionally, balancing may require discharging or charging individual cells to bring them to a similar level.
Deep Cycling:
Deep cycling entails discharging the battery pack to a very low level and then fully recharging it. This process can help break down crystalline formations that might have formed on the electrodes of the battery cells, contributing to reduced capacity. However, it’s essential to carry out deep cycling cautiously and under controlled conditions to prevent further damage to the battery cells.
Pulse Charging:
Pulse charging involves applying short bursts of higher voltage or current to the battery cells. This process can help break down certain types of deposits or buildups that might have formed on the cell electrodes. Consequently, careful control of the pulses is necessary to prevent overheating or damaging the cells.
Temperature Control:
Temperature has a significant impact on battery performance and longevity. Reconditioning processes often require careful temperature management to prevent overheating during charging and discharging cycles. Consequently, maintaining the appropriate temperature is essential for successfully reconditioning the battery.
Charge and Discharge Algorithms:
The reconditioning process often requires using specialized charge and discharge algorithms designed to rejuvenate weak cells. These algorithms can vary depending on the battery chemistry and the specific issues being addressed. Therefore, tailoring the algorithms to the battery’s needs is a crucial aspect of the reconditioning process.
Monitoring and Testing:
Throughout the reconditioning process, use diagnostic equipment to closely monitor the battery pack. This helps ensure that the process is proceeding as intended and that no further damage is occurring to the cells. Consequently, continuous monitoring is a critical aspect of the reconditioning procedure.
Final Evaluation:
After completing the reconditioning process, you should test the battery pack again to assess its performance and capacity improvements. If the reconditioning was successful, the battery pack should exhibit increased capacity and improved overall performance. Therefore, conducting post-reconditioning testing is essential to confirm the effectiveness of the process.